(1).png)
EXPLANATION
Work to do
Precious metals in electronic cards that have been removed from electronic devices or discarded during production will be separated as a result of physical and chemical
processes.
For waste electronic cards, recycling machines with a daily capacity of 5 tons will be manufactured, assembled on-site, put into operation and personnel will be trained.
Metals to be recycled are Copper, Lead, Tin, Gold, Silver, Palladium and Platinum.
Implementation Stages and Return on Investment
After the prepayment is made to the T.C. company, the production of recycling machines will start and the production will be completed in 180 days.
It will take 30 days to assemble the machines in their places in the facility. Staff will be trained during assembly.
Production will start after 180 + 30 = 210 days ( 7 months ).
Production will take 152 days. ( 5 tons of production will be made per day, 760 tons of production will be made in 152 days )
Buyers of all products are always ready. In exceptional circumstances, the time may be extended.
TOTAL TIME : 12 months ( 180 + 30 + 152 = 362 days )
NOTE ;
Since machinery was invested during the establishment of the facility, after the 2nd year, only raw materials will be purchased and mass production will be carried out, therefore
each recycling process will provide profit in a very short time.
.jpg)
AREAS WHERE THE INVESTMENT WILL BE USED ( For 5 Tons of Production per Day )
Machinery - October Pan and Electrical Infrastructure: 1.342.000 € (explanation is below)
Mill - 300 kwa : 300.000 € ( Spindle system 1 shreyer and 1 mill, Plastic separator, Capacity 1 to 3 days per day )
Induction furnace 200 kwa, 50 kg capacity : 45.000 €
Induction oven, 10 kg capacity : 7.000 €
Induction oven, 1 kg capacity, 2200 degrees, for Platinum : 9.000 €
Cooler : 5.000 €
Molding : 4.000 €
Smoke Filter, 20 kwa : 30.000 €
Electrolysis, 300 kwa: 450.000 € (capacity 5 tons of board / day and 1000 kg of copper)
Refining, 20 kwa : 115.000 €
Waste Water System : 20 kwa : 50.000 €
Compressor 12 kW: 7.000 €
Analysis laboratory, 5 kW : 40.000 €
Xrf : 30.000 €
Project + Personnel Training + Technical Knowledge Transfer: 250.000 €
Preparation of the building for production: 300.000 € (Electricity, water, ventilation, floor covering operations and obtaining licenses)
Non-production machinery and equipment: 100.000 € (forklift and transport vehicles to be used in the system)
Raw Material Stock: 1.500.000 € (explanation is below)
In order to produce at least 5 tons per day, the 30-day raw material stock amount should be 5 tons x 30 Days = 150 tons.
Raw material requirement for 30 days 150 tons x 1 ton card price 10.000 € = 1.500.000 € stock is required.
Margin of Safety : 300.000 €
TOTAL INVESTMENT PRICE: 3,534.000 €
FINANCIAL ANALYSIS
Investment Price : 3,534.000 €
Turnover : 11.400.000 € ( 1 ton product sales price 15.000 € x 760 tons product sales = Turnover 11.400.000 € )
Cost : 7.866,000 € ( 1 ton electronic card purchase price 10.000 € + 1 tonne production cost 350 € = 10.350 € x 760 tons = 7.866,000 € )
Net Profit : 3.534.000 € (1 ton product sales price 15.000 € - 1 ton product cost 10.350 € = 1 ton product Net Profit 4.650 € x 760 tons of product = 3.534.000 € )
NOTE : 1 ton production cost: 350 € (explanation is below)
Chemical and electrical consumables: 200 €
Business personnel, 12 people, 25 days of work: 100 €
Building cost : 50 € ( Rent is 5.000 € + Cost per ton is 5.000 / 5 tons / 25 days = 40 € )
.jpg)
INFRASTRUCTURE
Preparation of Infrastructure
Before the assembly of the machines, electricity, lighting, ventilation, water installations and waste water systems should be prepared according to the machine layout project.
The installed electrical power should be 1500 kW. A minimum of 3000 m2 closed area is required for the machine park. Ceiling height should be at least 5.00 m.
The personnel who will work in the workplace must be present at the workplace when the machine assembly begins. The staff will be trained for 30 days.
At the end of 30 days, first trial production will be made, then production will begin.
On-the-job training of the personnel will continue for another 60 days. (force majeure may extend the time)
Raw Material Purchasing
Materials can be obtained from 4 main sources in the market.
1 - Purchasing cards from used electronic machines from scrap dealers.
2 - Bidding or purchasing cards from electronic machinery manufacturers that have not passed quality control or are overproduced.
3 - Purchasing outdated machines from banks and large companies (such as telekom, turkcell) by tender.
4 - Purchasing from abroad.
The raw material (cards) will be analyzed, the value of the valuable material in it will be determined, then the purchase will be made.
The raw material price can range from € 50 to € 25-30 thousand per ton. (variable according to the mineral value in the raw material)
SALES
Electrolytic Copper, Gold, Silver and Palladium produced and precious metals are products that are sold in cash and there is absolutely no shortage of markets.
Prices are determined instantly on the London stock exchange.
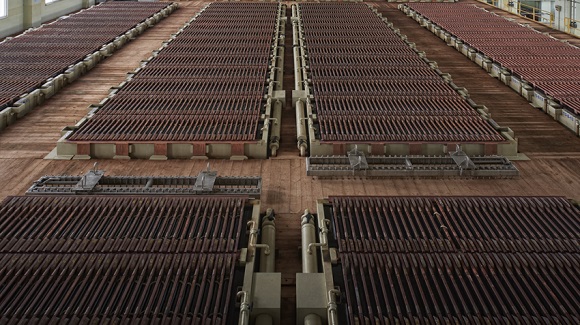
RESULTS OF THE RECYCLING PROCESS
A small amount of metal will be lost during physical operation (shredding, crushing, grinding and metal-plastic separation).
In chemical operation, since a recyclable system will be established, the loss of substance will be close to zero.
In copper electrolysis, all of the copper will be recovered as electrolytic copper with a purity of 999.8.
In the electrolysis of precious metals, all metals will be recovered in purities of 999.9 gold, 995 or 999 silver, palladium 999, platinum 999.
Flue gases will be made suitable for environmental conditions with filtering systems.
Acid vapors will be given to the chimney as neutral. Waste water will be purified from metal wastes and will be pH8, clear, brine, suitable for environmental conditions.
PHYSICAL OPERATION MACHINES
Mill
Shredder: It shreds the cards in 3 cm size.
Pre-grinder: It grinds the shredded material in 10 mm size.
Second grinder: It grinds the material to 2 mm and separates it into 4 as metal, magnetic metal, plastic and composite powder.
The system is supported by belt conveyors that transfer material from one machine to another.
Machine capacity and numbers will be shaped according to daily production capacity.
Induction Melting
100 kg capacity induction melting furnace (to be used for copper melting and anode castings).
10kg capacity induction melting furnace (to be used for melting gold and silver).
Induction melting furnace with 3 kg capacity and 2200 C heating (to be used for melting platinum and palladium).
Forming
It will be used in copper anode casting and for the preparation of precious metals in bar form by melting.
Filter
It is a filter with jet pulse system that will keep the smoke and metal oxides released during the melting process.
The system includes fume collector hoods, cooling cyclone, air suction fan and piping.
Compressor
It is a screw compressor with a storage capacity to meet the compressed air requirement of the facility.
CHEMICAL OPERATION MACHINES
Electrolysis
It is the system that allows the copper, which also contains precious metals, to be separated from the system as electrolytic pure copper.
The system includes rectifiers, electrolysis cell systems, automatic temperature controlled heating units and automatic controlled chemical dosing units.
Refining
The anode sludge value remaining from the copper, in mixed state, enables the metals to be obtained sequentially and in pure form by chemical operations.
It is a steam washing system that provides 100 kg rotary reactor, 50 kg rotary reactor, 10 kg rotary reactor and their solid-liquid separation, filtration systems
and neutral discharge of acid vapors under environmental conditions.
Waste water
It ensures that the metals in acidic and metalic waste waters are recycled and the water is discharged as pH 8 and clear salty water under environmental conditions.
It has a daily capacity of 10 tons and the whole operation will be done under automatic control.
Analysis Lab
It is an analysis laboratory with cupellation system that will make sensitive analyzes of precious metals produced by metal quantity analysis of cards.
Xrf Analyzer
It will be used to see the approximate values of all kinds of metals quickly.
WARRANTY PERIOD
The warranty period of the materials is one year.
The knives and sieves of the mills and the resistances working in the electrolysis heaters are not covered by the warranty, they are within the scope of consumables.
.jpeg)
.PNG)
COPPER ELECTROLYSIS SYSTEM
Important note;
In the copper electrolysis system, a new method has been developed, tried and successful by us, and the method has been patented.
Copper was melted and eliminated anode casting, copper was directly ground, electroplated while copper was in granule and/or powder form.
In the cathode, the method of obtaining cathodic copper sheet is used.
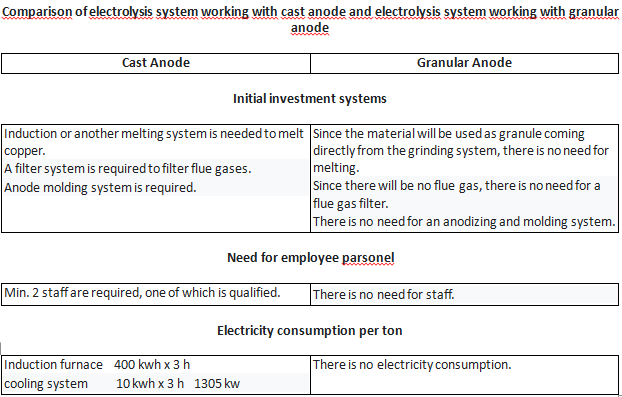
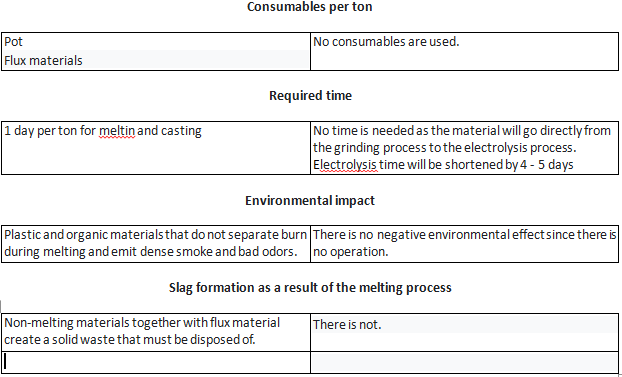
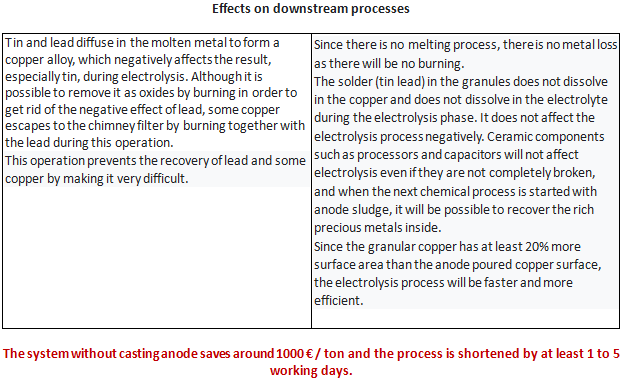
COUNTRIES SERVED
.PNG)
PROJECT REGION - ISTANBUL
.jpg)
WHY INVEST IN ISTANBUL ?
A GLOBAL CITY THAT CAN ACHIEVE BUSINESS GOALS FAST
Istanbul's economy is bigger than 130 countries
Continuous and fast growing dynamic market
Favorable entrepreneurship and investment climate
Cost-effective and qualified workforce
Productive private sector
Strong infrastructure
The city lives 24 hours
Ranked 1st in the world in terms of accessibility.. Strategically located between Europe, Middle East, Middle Asia and Gulf countries.
.jpg)
ABOUT INVEST IN TURKEY .jpg)
.jpg)
ABOUT TURKISH CITIZENSHIP
T.R. Conditions for becoming a citizen
Buying real estate for 400 thousand dollars and not selling it within 3 years,
To make a commercial investment of 500 thousand dollars,
To create employment for 50 people,
Opening a $500,000 bank deposit account and keeping it in a bank or government account for three years.
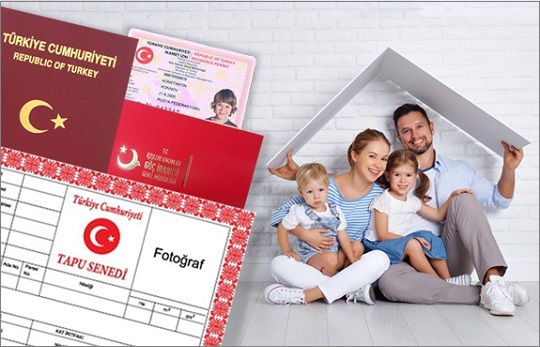